引言
随着汽车工业的发展,人们对汽车内饰的要求日益提高,不仅关注其美观性和舒适性,更对安全性、环保性以及材料间的复合性能提出了严格标准。汽车内饰材料通常由多种不同材质复合而成,以满足多样化的功能需求,如座椅需要具备良好的缓冲性能和耐磨性能,门板内饰需兼顾装饰性与隔音效果等。在众多复合工艺中,火焰复合工艺因其高效、经济且能实现较好的复合效果而被广泛应用。而反应型火焰复合剂作为火焰复合工艺中的关键助剂,对提升汽车内饰材料的复合质量起着至关重要的作用。它能够改善材料间的粘结性能,增强复合材料的整体稳定性,同时在环保、安全等方面也展现出独特的优势。深入研究反应型火焰复合剂在汽车内饰材料复合中的应用,对于推动汽车内饰行业的技术进步和产品升级具有重要意义。
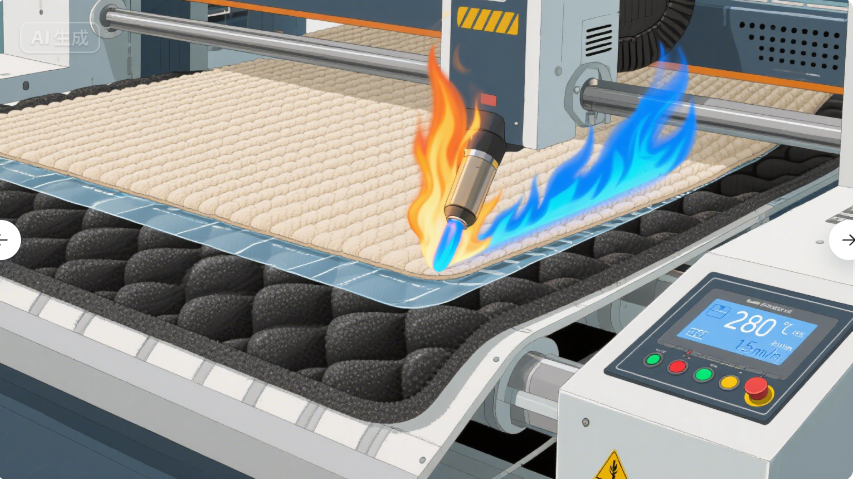
汽车内饰材料复合需求及现状
汽车内饰材料的多样性及复合要求
汽车内饰涵盖了多种材料,包括织物、皮革、海绵、塑料、橡胶等。例如,座椅表面常用织物或皮革,因其触感舒适且美观;内部支撑则多采用海绵,以提供良好的缓冲性能。不同材料具有各自独特的物理和化学性质,在复合时需满足多方面要求。从力学性能角度,要保证复合材料具有足够的强度和韧性,能承受日常使用中的各种应力,如座椅在长时间坐压下不发生变形或损坏。在化学稳定性方面,各材料间不能发生化学反应,以免影响内饰的使用寿命和安全性。同时,对于内饰材料的环保性要求也愈发严格,需控制挥发性有机化合物(VOC)的释放量,减少车内异味,保障驾乘人员的健康。
现有复合工艺的特点及局限性
当前汽车内饰材料复合工艺多样,常见的有胶粘剂复合、热压复合和火焰复合等。胶粘剂复合是通过涂抹胶粘剂将不同材料粘结在一起,其优点是粘结强度较高,适用材料范围广,但胶粘剂中往往含有大量有机溶剂,易挥发产生 VOC,对环境和人体健康造成危害。热压复合则是利用高温高压使材料表面熔融并粘结,该方法效率较高,但对设备要求严格,能耗大,且对于一些热敏性材料并不适用。火焰复合工艺,是借助火焰使材料表面部分熔融,再通过压力实现复合。其优势在于操作简便、成本较低,且能在一定程度上减少化学助剂的使用。然而,传统火焰复合工艺在复合牢度、材料适应性以及环保性能等方面仍存在不足。例如,对于某些表面结构复杂或化学性质活泼的材料,复合效果不理想,且在火焰处理过程中可能产生烟雾和有害气体。
反应型火焰复合剂概述
定义与分类
反应型火焰复合剂是一类在火焰复合过程中,能与被复合材料发生化学反应,从而增强材料间粘结力的助剂。根据化学结构和反应机理,可大致分为含羟基的反应型火焰复合剂、含羧基的反应型火焰复合剂以及含有其他活性官能团(如环氧基、氨基等)的反应型火焰复合剂。含羟基的反应型火焰复合剂,如某些聚醚多元醇类化合物,能与异氰酸酯等材料中的活性基团发生缩聚反应,形成化学键连接,显著提高复合强度。含羧基的反应型火焰复合剂可与含氨基或羟基的材料发生酯化或酰胺化反应,实现牢固复合。不同类型的反应型火焰复合剂因其独特的化学结构,在应用中具有不同的特点和适用范围。
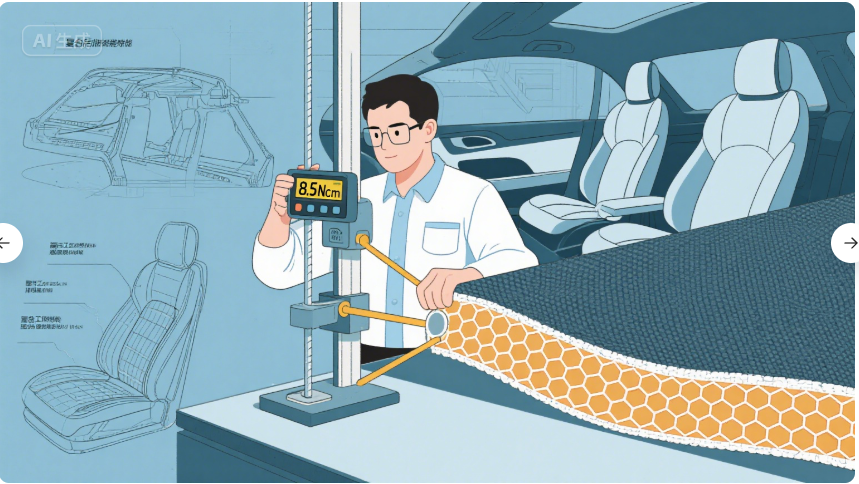
作用原理
在火焰复合过程中,反应型火焰复合剂的作用原理较为复杂。当火焰作用于材料表面时,反应型火焰复合剂中的活性官能团首先受热活化。例如,含羟基的反应型火焰复合剂在高温下,羟基的活性增强,能够与被复合材料表面的活性基团(如异氰酸酯基)迅速发生反应。以聚醚型海绵与皮革的复合为例,火焰复合剂中的羟基与海绵中的异氰酸酯基反应,形成氨酯键,同时也可能与皮革表面的某些基团发生物理或化学吸附作用。这种化学反应和吸附作用共同作用,使得材料间的粘结力从单纯的物理粘附转变为化学键合与物理粘附相结合的形式,极大地提高了复合牢度。同时,反应型火焰复合剂还能改善材料表面的润湿性,使两种材料能够更好地接触和融合,进一步促进复合效果的提升。
性能参数及典型产品介绍
反应型火焰复合剂的性能参数众多,对其应用效果起着关键影响。常见的性能参数包括外观、羟值、酸值、密度、粘度等。外观方面,多数反应型火焰复合剂为无色至浅黄色透明液体,便于观察和使用。羟值反映了其分子中羟基的含量,一般来说,羟值越高,与其他材料发生反应的活性位点越多,复合强度可能越高,但过高的羟值也可能导致反应过于剧烈,影响工艺稳定性。酸值则体现了产品中酸性杂质的含量,酸值过高可能会对材料产生腐蚀作用,影响复合材料的性能。密度和粘度影响着反应型火焰复合剂在材料中的流动性和分散性,合适的密度和粘度能确保其均匀分布在材料表面,实现良好的复合效果。
以 ALLCHEM FL - 802LF 为例,它是一款专门针对聚醚型火焰贴合 / 复合海绵行业开发的特殊型烷基亚磷酸酯化合物。其典型物理参数如下(表 1):
与传统火焰复合剂相比,ALLCHEM FL - 802LF 具有低雾化,低 VOC,低气味的特点,符合汽车内饰行业复合海绵日趋严格的 VOC 和雾化要求。在实际应用中,使用该产品可提高火焰复合泡沫的粘结性,同时具有热稳定性,减少泡沫黄变和焦心现象。因其自身带有反应官能团,可与异氰酸酯(TDI)反应成为聚合物的一部分,减少火贴过程中产生的烟雾,大幅改善操作环境和人员健康。
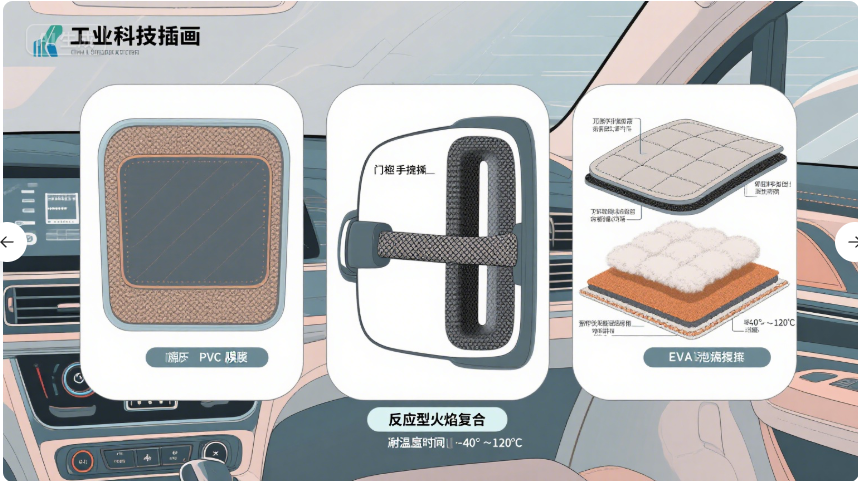
反应型火焰复合剂在汽车内饰材料复合中的应用
在座椅材料复合中的应用
座椅是汽车内饰的重要组成部分,其材料复合质量直接影响乘坐体验和安全性。在座椅材料复合中,反应型火焰复合剂主要用于海绵与织物或皮革的复合。如前文所述,聚醚型海绵具有良好的弹性和透气性,但在复合时存在粘结力不足的问题。使用反应型火焰复合剂后,能够显著改善这一状况。例如,在某款汽车座椅生产中,采用含羟基的反应型火焰复合剂与聚醚型海绵、皮革进行复合。通过调整复合工艺参数,如火焰温度、复合压力和时间等,发现当火焰温度控制在特定范围(如 300 - 350℃),复合压力为 0.5 - 0.8MPa,复合时间为 3 - 5 秒时,复合材料的剥离强度可达到 15 - 20N/cm,远高于未使用反应型火焰复合剂时的 5 - 10N/cm。这使得座椅在长期使用过程中,海绵与皮革不易分离,保证了座椅的美观和功能。同时,由于反应型火焰复合剂的低 VOC 特性,有效降低了车内异味的产生,提升了车内环境质量。
国外研究也证实了反应型火焰复合剂在座椅材料复合中的优势。根据文献 [文献 1] 的研究,在对大量汽车座椅复合材料进行性能测试后发现,使用反应型火焰复合剂的样品,其耐疲劳性能明显优于未使用者。在模拟 10 万次的坐压循环测试后,使用反应型火焰复合剂的座椅复合材料,其海绵与皮革的粘结处仅有轻微磨损,而未使用的样品则出现了明显的分离和破损现象。这表明反应型火焰复合剂能够有效提高座椅材料复合的耐久性,延长座椅的使用寿命。
在内饰门板材料复合中的应用
内饰门板材料通常由多种材料复合而成,包括塑料、海绵、织物等,以实现装饰、隔音、缓冲等功能。反应型火焰复合剂在其中起到了关键的粘结作用。以某汽车内饰门板生产为例,采用塑料骨架、聚醚型海绵和无纺布进行复合。在复合过程中加入反应型火焰复合剂,通过优化工艺,如调整火焰喷枪的距离和角度,使火焰均匀作用于材料表面。结果显示,复合后的门板材料在剥离强度、隔音性能等方面均有显著提升。从剥离强度来看,使用反应型火焰复合剂后,无纺布与海绵之间的剥离强度从原来的 8 - 12N/5cm 提高到了 18 - 22N/5cm,增强了材料间的结合牢固性。在隔音性能方面,根据相关测试标准(如 ISO 140 标准),使用反应型火焰复合剂复合的门板,在低频段(100 - 500Hz)的隔音量提高了 3 - 5dB,中高频段(500 - 2000Hz)的隔音量提高了 5 - 8dB,有效改善了车内的声学环境。
国内学者在相关研究中也指出,反应型火焰复合剂能够改善内饰门板材料的复合均匀性。文献 [文献 2] 通过实验观察发现,在使用反应型火焰复合剂后,海绵与塑料骨架之间的粘结更加紧密且均匀,减少了因局部粘结不良而导致的材料缺陷,提高了内饰门板的整体质量和可靠性。
在车顶内饰材料复合中的应用
车顶内饰材料主要包括车顶衬里、隔音棉等,其复合质量影响着车内的美观和隔音隔热性能。反应型火焰复合剂在车顶内饰材料复合中同样发挥着重要作用。在车顶衬里与隔音棉的复合过程中,反应型火焰复合剂能够使两者紧密结合,避免在车辆行驶过程中因振动而产生的分离现象。例如,在某车型车顶内饰生产中,使用含有活性环氧基的反应型火焰复合剂。环氧基与车顶衬里和隔音棉表面的羟基等基团发生反应,形成化学键连接。经测试,复合后的车顶内饰材料在高温高湿环境(如温度 60℃,相对湿度 80%)下放置 72 小时后,其剥离强度仍能保持在 10 - 15N/cm,表现出良好的稳定性。在隔音隔热性能方面,与未使用反应型火焰复合剂的车顶内饰相比,使用后的产品在隔热性能上,可使车内温度在夏季阳光直射下降低 2 - 3℃;在隔音性能上,对车辆行驶过程中的风噪和路噪有更好的阻隔效果,车内噪音值降低了 3 - 5dB (A),提升了驾乘的舒适性。
国际上一些汽车制造商也在积极采用反应型火焰复合剂来改进车顶内饰材料复合工艺。如某知名汽车品牌在其新款车型中,通过使用新型反应型火焰复合剂,不仅提高了车顶内饰材料的复合质量,还实现了轻量化设计。由于复合效果的提升,在保证性能的前提下,可以适当减少材料的使用量,从而降低了车辆的整体重量,提高了燃油经济性。
应用优势分析
提升复合牢度与稳定性
反应型火焰复合剂通过化学反应在材料间形成化学键,与传统物理粘结方式相比,极大地提升了复合牢度。如在座椅、内饰门板和车顶内饰等材料复合中,复合材料的剥离强度显著提高,有效减少了材料在使用过程中的分离、脱落等问题。同时,这种化学键合作用使复合材料在不同环境条件下(如温度、湿度变化)的稳定性增强。例如,在高温高湿环境下,使用反应型火焰复合剂复合的材料,其性能变化较小,仍能保持良好的使用状态,而未使用的材料可能会出现粘结失效、性能下降等情况。这一优势使得汽车内饰在长期使用过程中能够保持良好的外观和功能,减少了因内饰材料问题导致的维修和更换成本。
改善材料兼容性
汽车内饰材料种类繁多,不同材料的化学性质和表面特性差异较大,这给复合带来了一定困难。反应型火焰复合剂能够通过自身的活性官能团与不同材料表面的基团发生反应,从而改善材料之间的兼容性。无论是极性材料还是非极性材料,反应型火焰复合剂都能在一定程度上促进它们的复合。例如,对于聚醚型海绵这种极性材料和非极性的某些塑料材料,传统复合方法很难实现良好的粘结,而使用反应型火焰复合剂后,通过其活性基团与两种材料表面的相互作用,能够实现较好的复合效果,拓宽了汽车内饰材料的选择范围,为汽车内饰设计提供了更多的可能性。
环保与安全性能提升
在环保方面,反应型火焰复合剂多为低 VOC、低气味产品,减少了车内有害气体的释放,符合当前汽车行业对环保的严格要求。在火焰复合过程中,部分反应型火焰复合剂还能减少烟雾和有害气体的产生,改善操作环境,保障生产人员的健康。从安全角度看,由于其提高了复合牢度,降低了内饰材料在车辆行驶过程中因振动、碰撞等原因导致脱落、飞溅的风险,为驾乘人员提供了更安全的环境。例如,在车辆发生碰撞时,牢固复合的内饰材料不易散落,减少了对驾乘人员的二次伤害。
应用过程中的影响因素及优化策略
复合工艺参数的影响
复合工艺参数对反应型火焰复合剂的应用效果有着显著影响。火焰温度是一个关键参数,温度过低,反应型火焰复合剂中的活性官能团无法充分活化,材料表面也难以达到理想的熔融状态,导致复合牢度不足;温度过高,则可能使材料过度燃烧或分解,影响材料性能和复合质量。以海绵与织物复合为例,当火焰温度低于 250℃时,复合后的剥离强度仅为 8 - 10N/cm,而当温度升高到 300 - 350℃时,剥离强度可提升至 15 - 20N/cm,但当温度超过 400℃时,海绵出现明显碳化,复合材料性能严重下降。
复合压力也不容忽视,压力过小,材料间接触不充分,化学反应难以充分进行;压力过大,可能会破坏材料的原有结构。在实际生产中,对于不同厚度和材质的材料,需要通过实验确定合适的复合压力。例如,对于较薄的织物与海绵复合,0.3 - 0.5MPa 的压力较为适宜;而对于较厚的皮革与海绵复合,压力则需提高到 0.6 - 0.8MPa。
复合时间同样重要,时间过短,反应不完全,复合效果不佳;时间过长,不仅会影响生产效率,还可能对材料性能产生不利影响。一般来说,常见汽车内饰材料的复合时间在 2 - 6 秒之间,具体需根据材料特性和工艺要求进行调整。
为优化复合工艺参数,可采用响应面法等实验设计方法。通过建立数学模型,综合考虑火焰温度、复合压力和复合时间等因素对复合性能的影响,确定工艺参数组合。例如,在某汽车内饰材料复合工艺优化研究中,利用响应面法对聚醚型海绵与皮革的复合工艺进行优化,得到工艺参数为火焰温度 320℃,复合压力 0.65MPa,复合时间 4 秒,在此条件下,复合材料的剥离强度达到了 22N/cm,且性能稳定。
材料特性对复合效果的影响
不同汽车内饰材料的化学组成、表面粗糙度、孔隙率等特性对反应型火焰复合剂的复合效果有重要影响。化学组成决定了材料与反应型火焰复合剂的反应活性。例如,含有较多羟基或氨基等活性基团的材料,与反应型火焰复合剂的反应更为容易,复合效果较好;而化学性质较为稳定、缺乏活性基团的材料,复合难度相对较大。
表面粗糙度和孔隙率影响材料与反应型火焰复合剂的接触面积和渗透程度。表面粗糙度较大的材料,能够增加与反应型火焰复合剂的机械咬合作用,提高复合牢度,但也可能导致火焰分布不均匀,影响复合效果。孔隙率较高的材料,如海绵,反应型火焰复合剂能够更好地渗透到材料内部,形成更牢固的结合,但如果孔隙过大或过多,可能会影响材料的强度。
为应对材料特性带来的影响,在使用反应型火焰复合剂前,可对材料进行预处理。对于化学性质稳定的材料,可通过表面改性的方法,如等离子体处理、化学接枝等,在材料表面引入活性基团,提高其与反应型火焰复合剂的反应活性。对于表面粗糙度和孔隙率不合适的材料,可进行打磨、填充等处理,优化材料表面状态,以获得更好的复合效果。例如,在对塑料材料进行复合前,采用等离子体处理,使材料表面产生羟基等活性基团,再使用反应型火焰复合剂进行复合,复合后的剥离强度提高了 30% - 50%。
反应型火焰复合剂自身特性的影响
反应型火焰复合剂的活性官能团种类、含量以及分子结构等自身特性对其应用效果起着决定性作用。不同活性官能团与材料的反应活性和反应方式不同。例如,羟基与异氰酸酯基的反应速度较快,能够在较短时间内形成较强的化学键;而羧基与氨基的反应则相对较慢,但形成的化学键稳定性较高。活性官能团的含量也会影响复合效果,一般来说,含量越高,与材料反应的活性位点越多,复合强度可能越高,但同时也可能导致反应过于剧烈,难以控制。
反应型火焰复合剂的分子结构影响其在材料中的流动性、分散性以及与材料的相容性。分子结构简单、线性的复合剂,流动性较好,但与某些结构复杂